A Look Into Smart Factories: A Model of IIoT Innovation
Organizations worldwide are integrating the internet of things (IoT) closely into how they do business, a move that is as much about keeping up with the rest of the world as it is about improving operations. Such a large part of the IoT has been dedicated to industries that this aspect is given a further designation: the industrial internet of things (IIoT).
The IIoT prominently exemplifies the convergence of information technology (IT) and operational technology (OT). Traditionally, IT and OT coexisted within most organizations but functioned separately. Advancements in technology that have made the IoT possible, including wireless sensors, radio-frequency identification (RFID) tags, advanced data analytics, and ubiquitous computing, have also made possible the integration of IT and OT systems, thereby extending each of the two technologies’ functions.
The IIoT is at the heart of changes being implemented in many industries, and it is closely associated with what is being hailed as the fourth industrial revolution or Industry 4.0, the current trend in manufacturing. The IIoT and Industry 4.0 present concepts and realities that advancements in technology have created, many of which can be better understood in the context of one of their embodiments: the smart factory.
What are smart factories and what makes them work?
Smart factories vary considerably as companies that use them employ components and processes that are specific to their respective products. However, smart factories can still be distinguished by certain shared characteristics that set them apart from conventional factories.
A general description of smart factories is that they involve highly digitized and connected manufacturing to perform extended functions beyond automation. Network connectivity allows a smart factory to use data gathered from its environment as basis for a more autonomous, adaptive, and flexible response to whatever changes that may happen in and around it. In other words, smart factories are context-aware.
For such capabilities to function for a smart factory, it must be supported by a background system that takes information from both the virtual and physical worlds surrounding it. Information circulating within a smart factory can therefore range from simulation models (virtual) to tool conditions (physical). This fusion of physical and virtual world information is made possible by cyber-physical systems (CPSs) and IoT systems working together to extend the capabilities of machines on the factory floor:
- Cyber-physical systems. CPSs such as robots and process control systems entail the integration of physical, computational, and network processes, allowing each process to have an effect on the others. CPSs are largely responsible for creating the virtual copies of physical processes and surroundings.
- IoT systems. Whereas the focus in CPSs is on how physical, computational, and network processes affect one another, the focus in IoT systems is on connecting smart objects or devices such as sensors and automated controls to a network to extend their functions. In the context of a smart factory, the IoT systems link the CPSs together.
The combination of CPSs and IoT systems gives a smart factory certain characteristics that may be best described by four of the six design principles of Industry 4.0. Derived from a literature review on Industry 4.0, these principles serve as a guide for companies and manufacturers in their efforts to build a more digitized production chain:
- Interoperability. One of the essential characteristics of the IoT, this enables machines and other devices that are essential to the production chain of a smart factory to communicate with one another and with the network.
- Virtualization. With the ability of CPSs to monitor physical processes, a smart factory is able to simulate or create a virtual copy of the real world surrounding it. This enables the smart factory to integrate inputs from the virtual and physical worlds. As a result, the smart factory is able to act in a highly context-specific way using information from the past (simulations) and present (real-time monitoring). This also allows a more transparent view of the entire manufacturing process for operators.
- Decentralization. In a smart factory, control isn’t limited to just a single computing unit. Because the CPSs function independently, a smart factory can be more flexible and optimized in solving problems.
- Real-time capability. A smart factory has the capability to react to issues that may happen on the fly. Data is monitored in real time so that the factory can respond to what is happening around it. This ability to constantly monitor its processes also enables the smart factory to notice and even predict anomalies that otherwise might lead to more serious problems.
Beyond the factory floor, a smart factory is characterized by its extensive influence on and connection with other parts of its production chain. A smart factory can work best within the confines of an equally smart and connected enterprise, where there is a sustained connection between all departments, extending even outside of the enterprise to customers and suppliers.
What are the advantages of smart factories?
A recent report on the future of manufacturing suggests that smart factories are in the future plans of manufacturers, as top spending priorities of manufacturers include smart factory components: IoT solutions, advanced robotics, advanced analytics, and cybersecurity. The main advantages of smart factories may be enough to persuade manufacturers to incorporate these facilities into their production chains:
- Provide well-rounded information from automated data. Managers or decision-makers in manufacturing companies will find it easier to access a wealth of information for advanced production analytics, which can be used for implementing plans and measuring performance.
- Improve quality of products. Aspects of smart factories, such as digital twins (virtual equivalents of physical assets and processes), enable the constant monitoring of the quality of products before they are released in the market. The abundance of data also helps detect patterns that affect the quality of the products.
- Lower cost of production. The self-optimization characteristic of smart factories helps streamline processes and provides feedback for manufacturers to identify redundant or counterproductive steps on the entire production chain.
- Offer predictive maintenance. The visibility of smart factories allows manufacturers to catch problems or maintenance issues before they create a significant effect on the rest of the equipment or the entire production chain. This aspect of smart factories also improves safety on the factory floor for employees by reducing the risk of accidents from malfunctioning equipment.
What are the challenges in implementing smart factories?
Despite the positives smart factories may bring to an enterprise, adopting their use is still a big choice to make. Even a small change in the manufacturing process can be a heavy decision for an enterprise, because at stake is the enterprise’s reputation with its customers as well as the quality and speed of its production. Fully implementing a smart factory, therefore, involves not only setting it up but also preparing for the challenges it may pose.
One of the more pressing challenges is the huge amount of data a smart factory entails. Because of this, the enterprise must have protocols and systems in place for the proper use and handling of such a large quantity of data before setting up a smart factory.
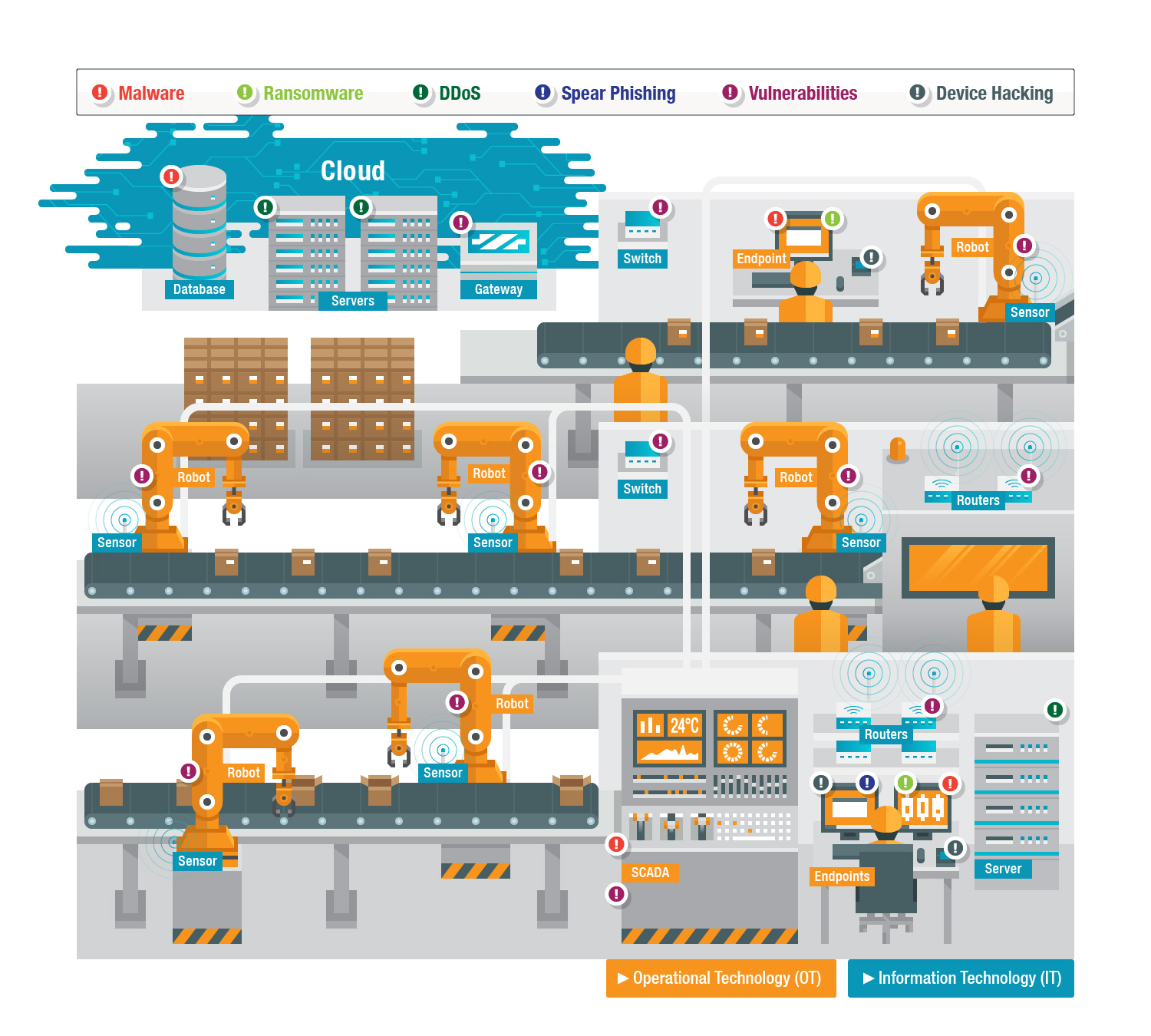
The convergence of IT and OT in a smart factory also expands the enterprise’s attack surface, which may not be always fully considered in traditional security measures, e.g., fragmented security solutions that may not always apply to OT. Because of this, the smart factory may be susceptible not only to operational problems but also to cyberattacks involving malware, ransomware, distributed denial of service (DDoS), spear phishing, vulnerabilities, and device hacking, among others.
[See: Integrating Security Into the IoT Strategy in the New Converged Environment]
Building a smart factory
Taking cues from the close integration of traditionally separate technologies (IT and OT, virtual and physical), companies looking into building smart factories must ensure the close cooperation between its IT and OT experts not only during the planning phase but all throughout the implementation of the smart factories.
Considering how smart factories are dynamic in nature, manufacturers must also continue development even after the smart factories are fully constructed. Even with the more autonomous production of these facilities, how the smart factories will fulfill the overarching company goals still remains in the hands of the company decision-makers.
Rounding off the preparation of smart factories are security solutions that must be closely integrated in the design of the facilities to support the transition toward them without being susceptible to threats that may arise from a wider attack surface. Departments that maintain IT and OT should work together to share their expertise to take right security posture across both technologies.
To fully realize the potential of smart factories, companies must understand that implementing them is a gradual process that mirrors the development that made smart factories possible in the first place. Manufacturing is one of the industries that showcase turning points in technological advancements, and the smart factory demonstrates a relatively recent innovation brought about by the IIoT, CPSs, and the many components that made both possible. Indeed, the general trend of development is the convergence and integration of technologies that traditionally existed in silos, and the consequent creation of a new space for further innovation.
Like it? Add this infographic to your site:
1. Click on the box below. 2. Press Ctrl+A to select all. 3. Press Ctrl+C to copy. 4. Paste the code into your page (Ctrl+V).
Image will appear the same size as you see above.
Recent Posts
- Unmasking Task Scams to Prevent Financial Fallout From Fraud
- Beware of MCP Hardcoded Credentials: A Perfect Target for Threat Actors
- Lessons in Resilience from the Race to Patch SharePoint Vulnerabilities
- LLM as a Judge: Evaluating Accuracy in LLM Security Scans
- The Silent Leap: OpenAI’s New ChatGPT Agent Capabilities and Security Risks